Refractories play a significant role in aluminium production and the production of other high-temperature materials. These refractories are nothing but a range of materials that offer the necessary thermal insulation and chemical and mechanical resistance during the production of aluminium and its alloys. The various equipment pieces used in aluminium production are lined with refractory materials to sustain high temperatures and resist chemical attacks. This allows the production process to be carried out safely and securely. Over the years, the refractory industry has made remarkable advancements. Today, it forms a crucial part of the ferrous and non-ferrous metal industry that forms the backbone of an economy.
Application of refractory materials in aluminium production:
Refractory materials are used for lining various containers and equipment pieces found in an aluminium smelter. These containers include:
- Reduction cells
- Melting furnaces
- Holding furnaces
- Casting equipment like moulds and ladles
- Transporting equipment like crucibles and troughs
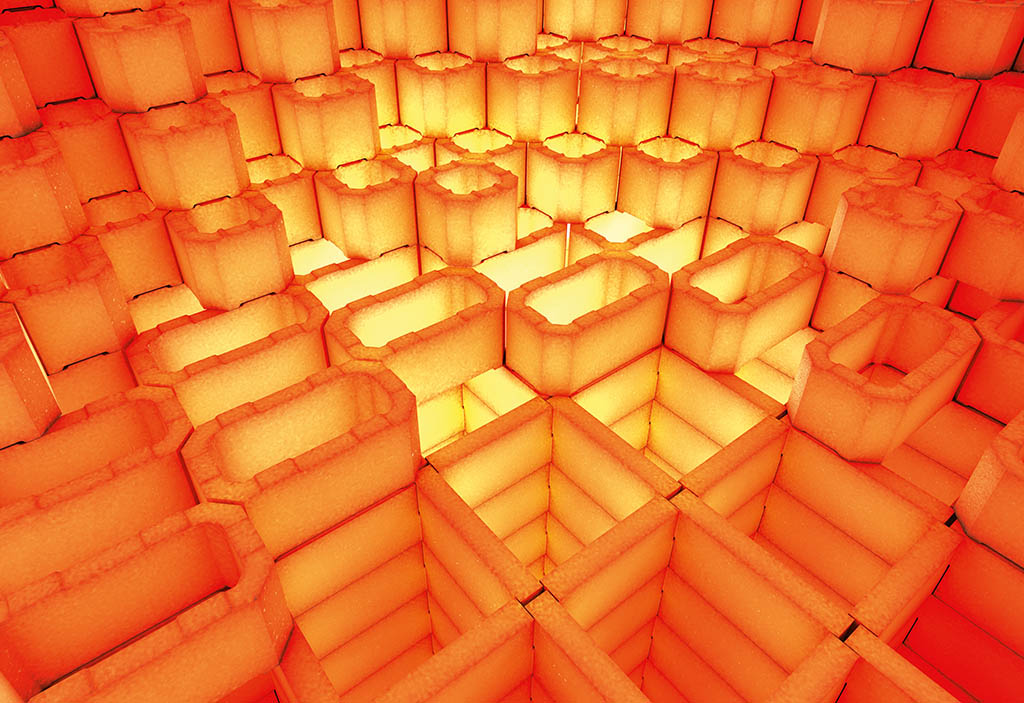
Types of refractories used in the aluminium industry
Different types of refractories are used in the aluminium industry, each with unique properties. Here are some of the most frequently used refractory materials:
- High-alumina refractories: These refractories are quite common in the aluminium industry. This is mainly because of their easy availability and enhanced thermal insulation properties.High alumina contains around 50-99% alumina. They can easily protect the furnaces from high temperatures, chemical attacks, and abrasion. High alumina also offers excellent thermal conductivity. It can protect the furnace from cryolite attack.
- Silicon carbide refractories: Silicon carbides are used to line the holding furnaces and crucibles. They offer excellent thermal resistance and high protection against abrasion and oxidation. The material also has high mechanical strength and chemical inertness. These refractories are produced from raw silicon carbide, which is synthesised at temperatures exceeding 2500°C through the reaction of silica with carbon.
- Mullite refractories: These are formed by the reaction of alumina and silica and offer good resistance to thermal shock and chemical corrosion. They have outstanding thermo- mechanical properties and a high stability level, making them appropriate for lining the ladles and furnaces. Mullite refractories have a high melting point of 1,840 °C. This makes
- Magnesia refractories: These are made from magnesia, graphite, antioxidants, and resin. They are primarily used in lining casting furnaces and ladles. They offer good thermal resistance to molten aluminium and slag but have poor thermal shock resistance. Magnesia refractories are also quite well-known for their high corrosion resistance properties.
Choosing the suitable refractory material for aluminium production
Here are some of the aspects that require consideration while choosing the refractories:
- Temperature resistance: The refractories should be able to withstand extremely high temperatures without getting degraded. They should also have excellent thermal insulation and thermal shock resistance properties.
- Mechanical strength: The refractory material should withstand mechanical wear and tear caused by the movement of molten aluminium and other materials inside the reduction cell. This will protect the cell from mechanical damage.
- Chemical resistance: Always go for one such refractory material highly resistant to the chemical attack of molten aluminium, cryolite, and other chemicals frequently used in aluminium production.
- Cost: You would want to spend little money on refractory materials. So, go for materials that are available at budget-friendly prices. The installation process should also be easy and inexpensive.
Future trends in refractories
Here are some of the latest developments in the refractory industry:
- Introduction of new refractories: Studies are being done to develop new refractory materials with advanced thermal and chemical resistance and better mechanical strength.
- Improved manufacturing process: Researchers are developing advanced manufacturing processes to improve the service life and quality of the refraction material.
- Increased focus on sustainability: The aluminium industry is implementing sustainable practices in production. As a result, there is an increased demand for environmentally friendly refractories.
To end with:
Refractories have a vital role to play in the aluminium production process. They allow for efficient and safe production of aluminium. So, if you are involved in aluminium production, make it a point to choose the right kind of refractories for the production process. Only then can you ensure seamless aluminium production from the available raw materials.