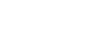
Or
By clicking Sign In, Join Free or Continue with Facebook, Linkedin, Twitter, Google, I agree to the Terms & Conditions and the Privacy Policy
For more than four decades, there has been a consistent upward trend in the use of aluminium in automotive production. This steady growth can be credited to the automotive industry’s ongoing pursuit of lighter vehicles, essential in electric vehicles (EVs). Vehicles with reduced weight need less electricity and can run on smaller or fewer batteries while maintaining a comparable range.
However, increased aluminium use has gained momentum recently, particularly since the pandemic. This can be attributed to stringent government measures to curb emissions, heavier vehicles due to increased consumer demand for larger models with additional features, and the multiple economic and performance benefits of aluminium frames and components.
Electric vehicles are a significant reason for this trend
The driving forces behind this surge in aluminium use are the ongoing trends of lightweight and electrification within the automotive sector. Mainly, the proliferation of electric vehicles (EVs) significantly contributes to this. A Battery Electric Vehicle (BEV) manufactured in Europe in 2022 contains an average of 283 kg of aluminium, contrasted with 169 kg in traditional internal combustion engine (ICE) cars.
This disparity highlights the pivotal role of aluminium in the movement of the automobile sector towards electric vehicles and sustainability. These electric vehicles represent the future of personal transportation, playing a crucial role in battling climate change and reaching sustainability targets.
The growth in aluminium usage in BEVs is anticipated to persist, with the average aluminium content projected to expand by 9.5% between 2022 and 2026, reaching 310 kg per vehicle. This growth can be attributed to various uses within BEVs, such as e-drive housing, battery pack housings, ballistic battery protection, and cooling plates. Moreover, aluminium's importance extends to electromobility charging infrastructure, used in crucial components like power cables and charging stations.
For BEVs, the weight of the batteries emerges as a crucial factor. Batteries are a substantial weight and the single most expensive component of a BEV. Aluminium presents a great solution due to its lightweight nature, boasting a density one-third that of steel while maintaining comparable strength. This unique property lets manufacturers use as little as 600 grams (or even less) of aluminium for each kilogram of steel normally used. Moreover, the advantages extend beyond weight reduction.
BEVs constructed with lightweight aluminium boast much faster charging times, better energy efficiency, and the potential for smaller battery packs. Smaller battery packs reduce cost, benefiting both automakers and end consumers alike. This synergistic relationship between aluminium use and BEV development drives technological improvements and facilitates consumer adoption.
By embracing aluminium lightweighting, vehicles achieve better handling, acceleration, quicker braking, reduced stress on brakes and suspension components, and the ability to bear heavier loads while towing or carrying cargo. Additionally, the inherent corrosion resistance of aluminium, along with its self-healing properties, is a step up for durability. When exposed to cracks or dents, aluminium naturally forms a protective oxide barrier. In the event of a crash, aluminium displays great energy absorption capabilities, leading to better crash performance and superior crush properties in comparison to steel.
Aluminium is crucial for all environmental-related endeavours
Crucially, aluminium's unique recyclability safeguards a sustainable future. This property ensures that the aluminium integrated into vehicles today remains viable for reuse in the future, even after a vehicle has reached the end of its life. Recycling aluminium is also very energy- efficient, using only approximately 5% of the energy required to produce primary aluminium from raw materials. This translates to a considerable reduction in carbon emissions, reaching up to 95%.
The World Economic Forum has estimated that adopting closed-loop recycling processes, which involve the continuous recycling of products to create new ones without them entering landfills, can yield a reduced energy consumption of up to 75%. These processes offer a range of benefits, including alleviating strain on natural resources, reducing pollution, and decreasing the need for landfill space. Adopting a closed-loop recycling process for scrap thus presents an immediate avenue for vehicle manufacturers to curtail their carbon emissions drastically.
As vehicles with more aluminium content reach the end of their lifecycle over the next decade, the implications for the automotive industry in minimising its carbon footprint are significant. The WEF suggests that by 2035, recycling 125 kilotons of aluminium scrap could result in a massive reduction of 950,000 tonnes in carbon emissions.
Several automotive manufacturers, including Toyota, Jaguar, Volvo, and Ford, have embraced leadership roles in this push. Volvo's goal is to become a circular business by 2040, committed to adopting closed-loop recycling for aluminium. On the other hand, Ford is actively integrating closed-loop practices by incorporating aluminium scrap into the production of its F-150 trucks.
As a result, there is no doubt that aluminium will play a pivotal role in propelling the automotive industry into an era of greater efficiency and product performance, all without compromising sustainability. No wonder they call it the metal of the future!