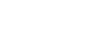
Or
By clicking Sign In, Join Free or Continue with Facebook, Linkedin, Twitter, Google, I agree to the Terms & Conditions and the Privacy Policy
Heavy metal production requires extreme energy consumption. Aluminium production is not exempt from this requirement. It is termed an energy-intensive industry in the global manufacturing sector, as it consumes around 17,000 kWh of power to manufacture 1 tonne of aluminium. This denotes that it has a comparatively high cost. However, the metal is very much appropriate for recycling. In simple words, it is stated that the strength of the chemical bond between aluminium and oxygen is notably stronger than the same bond between iron and oxygen. As a result of it, much more energy is needed to cleave the bond and form the metal.
For obvious reasons the production cost is substantial; what compensates the production cost here is the flexibility of the metal. Since Aluminum is the most malleable, non-ferrous metal and every byproduct or derivative of it is useful in some way or the other the production cost somehow gets navigable. From packaging to the airline, aluminium has got a colossal presence because of its lower electrical resistance and outstanding strength-to-weight ratio attributes. Fortunately aluminium is widely available after silicon and oxygen. Aluminium is mostly found as compound metals in about 270 assorted minerals. It concocts about 8% of the upper crust of the earth. Though technology has evolved towards attaining higher efficacy; however, aluminium production is one of the record energy-intensive processes marked by the global manufacturing business.
During the 70’s or early 80’s industrial aluminium cells used to get operated from 85-88% energy efficiency; while modern cells get delivered from 95-96% current efficiency.
Resources suggest that the major part of power is consumed in smelting furnaces which include processes like melting and reduction reactions. Aluminium is one of the most reactive metals. Thus, it cannot be extracted through any low-budget, chemical processes. Aluminium gets extracted from bauxite via alumina through electrolysis in the Hall-Héroult process. Only the mechanism of the aeroplane demands the primary or the purest form of aluminium. Beverage cans and automotive castings can be produced from the secondary form of aluminium. The electrical power utilized in primary aluminium production comprises power used for electrolysis by the Hall-Héroult processes (including rectification from AC to DC) and normal smelter auxiliaries (including pollution control equipment) up to the point where the liquid aluminium is tapped from the pots. Since it is an electro-intensive process, the carbon footprint of primary aluminium products highly depends on the source of electricity that it takes during production. In hydropower based regions 1-tonne aluminium production causes less than 4 tonnes of CO2 emission, whereas in coal-centric areas the volume of more than 20 tonnes per 1 tonne. Although, the recycling process releases 0.5 tonnes of CO2 per 1-tonne of goods produced. The carbon emission from recycles Aluminum trashes includes scrap collection, carriage, nomenclature, and re-melting.