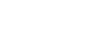
Or
By clicking Sign In, Join Free or Continue with Facebook, Linkedin, Twitter, Google, I agree to the Terms & Conditions and the Privacy Policy
Industry 4.0 describes technological and organizational changes in enterprises that include, among other things, digitization and automation of technological processes. This paper cites a state-of-the-art juncture in the industrial revolution that relies decisively on interconnectivity, automation, machine learning, and real-time data.
The technology succours to manage and reform all facets of manufacturing processes and supply chain. It grants access to real-time data and insights the requisite to make smarter, faster decisions on businesses that can eventually amplify the efficiency and profitability of your entire operation.
The term Industry 4.0 confines an assurance of a new industrial revolution—one that unifies ‘avant-garde’ manufacturing techniques with the Internet of Things (IoT) to develop manufacturing systems that are not only interconnected but communicate, analyse and use the information to navigate further intelligent action back in the physical world.
The fourth industrial revolution and the impact of the drivers and technologies behind Industry 4.0 have been looked at from the perspective of various sectors after the concept was launched. However, the aluminium industry may not be the first sector that comes to mind when people think of Industry 4.0, as advanced technology is abruptly proving its worth for supporting companies remain resilient in a challenging marketplace.
The adoption of digital solutions has helped smelters who use the electrolysis process to pull aluminium from its oxide boost productivity. Investing in technology has also proven to reduce problems by providing more insights; for instance, data analytics can give details about temperature and chemistry, allowing plant managers to make proactive changes to cut down on wasted time or money.
While sustainability has become a way for aluminium producers to mark themselves different in the market, IoT sensors give them an idea of how much electricity they use over a given period. It makes easier to lessen the consumption of electricity if required.
On one hand, there are companies that are facilitating these digital solutions in the form of Automation, Machine Learning, Artificial Intelligence, Robotics, IoT, Data Analytics, etc.; on the other hand, there are companies who are adopting these technologies and transforming themselves into Smart companies & factories.
It is an undeniable fact now that Industry 4.0 has proved to be an inevitable solution in the aluminium industry for the achievement of higher productivity at a lesser time and with a scanty workforce. Having experienced the robust outcome of the use of digitalisation and automation, a large number of aluminium smelters are increasingly harnessing the transformational potential of the 4th Industrial Revolution in a quest to position themselves as the ‘Smelter of the Future’.
A reasonable increase in investment has been the goal of the aluminium industry for the past few decades in order to increase capacity. But now, the reduction of greenhouse gas emissions is an additional objective of the industry, wherein Industry 4.0 platform technologies are foreseen to open up further opportunities. The integration of the Fourth Industrial Revolution is expected to optimise predictive control and operation and become a key driver for low-energy cells. In other words, Industry 4.0 is anticipated to progress aluminium smelting towards sustainable production.